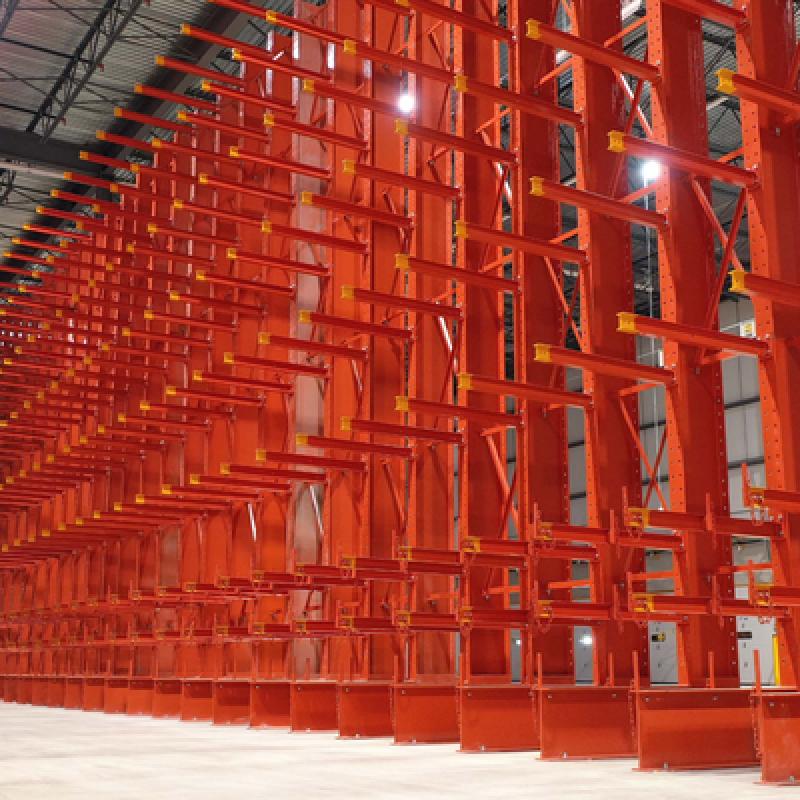
Why fire code compliance matters more than ever
Warehousing in Canada is expanding fast, driven by e-commerce, nearshoring, and increasing demand for flexible distribution space.
With this growth, many tenants are installing complex storage systems to maximize cubic capacity. But increased density and vertical storage heights bring higher fire risks, especially when flue spaces are obstructed or sprinklers are not properly designed for the storage configuration.
Failure to comply with fire protection codes can result in:
- Denied occupancy permits
- Delays in operational startup
- Voided insurance policies
- Costly retrofits post-inspection
- Significant risk to employee safety and inventory
As of 2025, updated guidelines are putting more pressure on the industrial sector to get racking and sprinkler design right the first time.
What's changing in the 2025 NFPA 13 Guidelines?
The 2025 edition of the NFPA 13 Standard for the Installation of Sprinkler Systems includes key changes affecting multiple-row and high-piled racking systems:
- Increased scrutiny of flue spaces
- New criteria for in-rack sprinklers
- Commodity classification clarity
- Updated obstruction guidelines
Real estate implications: What agents need to know
Industrial agents play a crucial role in helping clients assess whether a space is "move-in ready" or needs major infrastructure changes. Here’s how the new fire codes affect your leasing conversations:
- Clearance to ceiling
- Base building vs. tenant improvements
- Permitting considerations
- Warehouse classification
For tenants: Think fire safety before racking is installed
Many tenants focus first on racking layout and SKU velocity, only considering fire suppression at the end of the process. That’s a mistake.
Fire protection needs to be designed in parallel with racking—not after the fact. Key steps:
- Coordinate early with racking and fire protection vendors
- Don’t skip the pre-inspection walkthrough
- Avoid costly retrofit scenarios
Looking ahead: Building fire safety into asset strategy
As fire codes become more stringent and insurance standards tighten, fire protection is no longer a “compliance checkbox”—it’s a core component of industrial real estate value.
Whether you're a broker positioning a listing, or a tenant planning to expand or move in, understanding the current fire code is essential. Buildings that are proactively designed for fire code compliance—including ceiling clearances, sprinkler head spacing, and racking integration—offer reduced operational risk and improved leasing velocity.
The bottom line? Fire safety doesn’t start with the fire—it starts with smart planning, informed partners, and a deep understanding of the regulations that keep warehouses safe.
Fire code readiness checklist for agents and tenants
☐ Has the racking layout been reviewed for adequate flue spacing?
☐ Are in-rack sprinklers required based on storage type and height?
☐ Are the stored commodities correctly classified for fire risk?
☐ Is the existing sprinkler system compatible with the racking plan?
☐ Has the local Authority Having Jurisdiction (AHJ) approved the design?
☐ Have insurance requirements been reviewed for compliance?
☐ Has all equipment and layout documentation been submitted for permitting?
The insurance angle: What underwriters look for
Beyond fire code compliance, insurance providers are becoming increasingly stringent about how warehouses manage fire risk. A non-compliant racking system could increase premiums, reduce coverage, or disqualify a tenant entirely. Insurance underwriters typically assess factors such as:
- Height and density of pallet storage
- Type of commodities stored (plastics, aerosols, etc.)
- Sprinkler spacing and hydraulic capacity
- Whether flue spaces are consistently maintained
For landlords, ensuring that tenant racking is compliant protects not just one lease—it protects the asset’s insurability. For tenants, it’s about reducing liability and ensuring continuity of operations.
An example of non-compliance in action
Consider a 100,000 sq. ft. warehouse leased to a retail distributor. The tenant installs pallet racking to 32 feet high, unknowingly obstructing flue spaces with stretch-wrapped pallets and failing to include in-rack sprinklers for their plastic inventory. At final inspection, the local fire authority halts occupancy and mandates a full retrofit. The delay costs the tenant six weeks of lost operations and $120,000 in unplanned expenses. This is avoidable with proper upfront coordination and compliance planning.
Working with authorities having jurisdiction (AHJs)
Each municipality has its own fire department and permitting authority that interprets and enforces NFPA standards locally. These Authorities Having Jurisdiction (AHJs) must be consulted early. Some practical steps:
- Submit racking and sprinkler plans together, not separately
- Engage a certified fire protection engineer to stamp drawings
- Request a pre-submission meeting with the AHJ to clarify expectations
Early coordination avoids surprises late in the permitting process and often speeds up approval timelines.
Clarifying flue space measurements
A common point of confusion is what counts as sufficient flue space. According to NFPA 13:
- Transverse flue space should be 6 inches between each pallet load
- Longitudinal flue space should be 3 inches between back-to-back racks
- No solid shelving or shrink-wrap should obstruct these gaps
If these measurements can’t be consistently maintained—especially during restocking—then in-rack sprinklers are likely required.
A value-add for brokers and asset managers
Industrial brokers who understand fire code intricacies are positioned as trusted advisors. By helping clients evaluate warehouse suitability beyond square footage—such as ceiling height, sprinkler type, and racking layout—they can prevent costly oversights. For asset managers, investing in buildings that meet or exceed NFPA 13 standards can enhance leasing appeal, reduce downtime between tenants, and command stronger returns over time.
Talk to a racking expert
To ensure your warehouse racking and sprinkler design are compliant with the latest fire codes, contact North American Steel. Our experts can help assess your layout, coordinate with fire protection engineers, and provide fully code-compliant systems tailored to your space and inventory.
Contact us today here.